
INTRODUCTION
In August 2020, one Rome Grinding Solutions customer faced a critical challenge at several of its beef production plants. The company was required by USDA regulations to conduct hourly inspections of its meat grinders’ cutting assemblies, a task that significantly slowed production. Compounding this issue, the process of disassembling and reassembling the equipment required the use of a cumbersome twenty to thirty pound spanner wrench, which posed a safety risk to workers. The company needed a solution that would both streamline the inspection process and increase worker safety.
It turned to Rome Grinding Solutions, a leader in the meat grinding industry, to address these challenges. The result was the development of the Bolt-on Retaining Ring (BORR) system, an innovation that not only improved safety but also allowed the customer to minimize downtime and increase production efficiency.
THE Challenges
Beef production plants produce enormous quantities of meat daily. In compliance with USDA requirements, this customer had to inspect the cutting assemblies of its grinders once every hour. Each inspection took approximately ten minutes per grinder, a seemingly small disruption that added up quickly, particularly given the sheer volume of meat being produced. Over the course of a workday, this downtime represented a significant bottleneck in production.
Moreover, the safety concerns were real. The traditional method of tightening and loosening the retaining ring involved a heavy spanner wrench, which was difficult and dangerous for workers to handle. The customer’s innovation and automation teams sought a solution that would not only reduce downtime but also eliminate the need for such hazardous tools, thus improving workplace safety.
“The V2 BORR system was designed to use standard material castings, which lowered costs and ensured that the system remained within budget.”
The Solution: Rome’s BORR System
In response to these needs, Rome Grinding Solutions designed and developed the Bolt-on Retaining Ring (BORR) system. This innovative solution allowed for quick disassembly and reassembly of grinding equipment without the need for heavy tools, thereby addressing both production inefficiencies and safety risks.
The development of the BORR system followed a structured timeline:
Ryan Van Maasdam from Rome Grinding Solutions met with the customer to discuss the challenges and possible solutions. Rome immediately began designing the BORR system.
Less than a week later, Rome submitted the initial concept drawing for the BORR system, though an early challenge was finding a torque wrench capable of applying equal tension across all bolts.
A chance meeting at a gas station provided the solution. Van Maasdam was introduced to Air Automation Engineering, a company that manufactures programmable torque wrenches—exactly the tool needed for the BORR system to function as intended.
Within another month, Rome completed the V1 BORR assembly. Customer representatives visited Rome’s facility to inspect and approve the system.
Later that fall, the V1 system was installed at one of the customer’s production plants, marking the first successful implementation.
Based on feedback from the initial installation, Rome made several design modifications to improve the system over the next few months. The V2 BORR system was designed to use standard material castings, which lowered costs and ensured that the system remained within budget. By January, the V2 system was fully installed and optimized for production use.
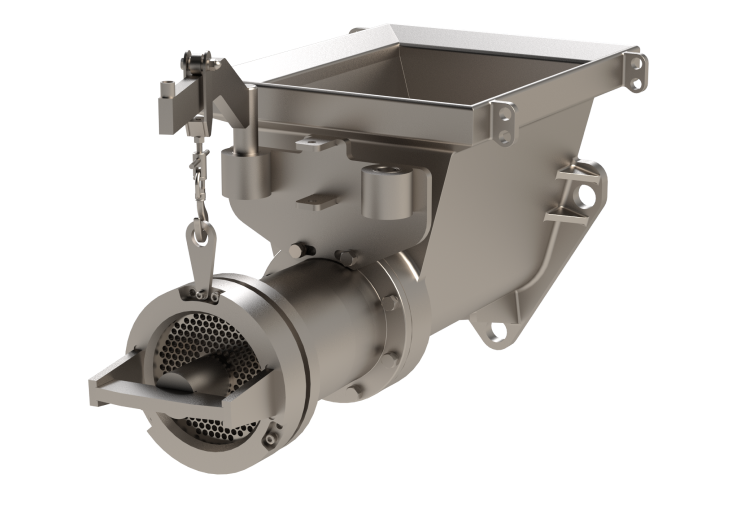
Results and Impact
Since the installation of the BORR system, the industrial beef producer has rolled it out across six of its largest ground beef production facilities, including locations in:
- Amarillo, TX
- Lexington, NE
- Dakota City, NE
- Holcomb, KS
- Joslin, IL
- Pasco, WA
The BORR system delivered significant improvements across Tyson’s operations:
Increased Production Efficiency: By drastically reducing the time needed for hourly inspections, the BORR system minimized downtime. This customer saw immediate gains in production throughput, with more meat being produced in less time. Given the scale of its operations, these time savings translated into substantial increases in daily production.
Enhanced Worker Safety: The BORR system eliminated the need for workers to use the heavy spanner wrenches that had previously been necessary to tighten and loosen the grinder’s retaining rings. This significantly reduced the risk of worker injuries and created a safer, more ergonomic working environment.
Cost Savings: Through the design revisions that led to the V2 system, Rome was able to standardize the use of materials, keeping production costs in check. This allowed the customer to implement the solution without exceeding budget constraints, further enhancing the value of the system.
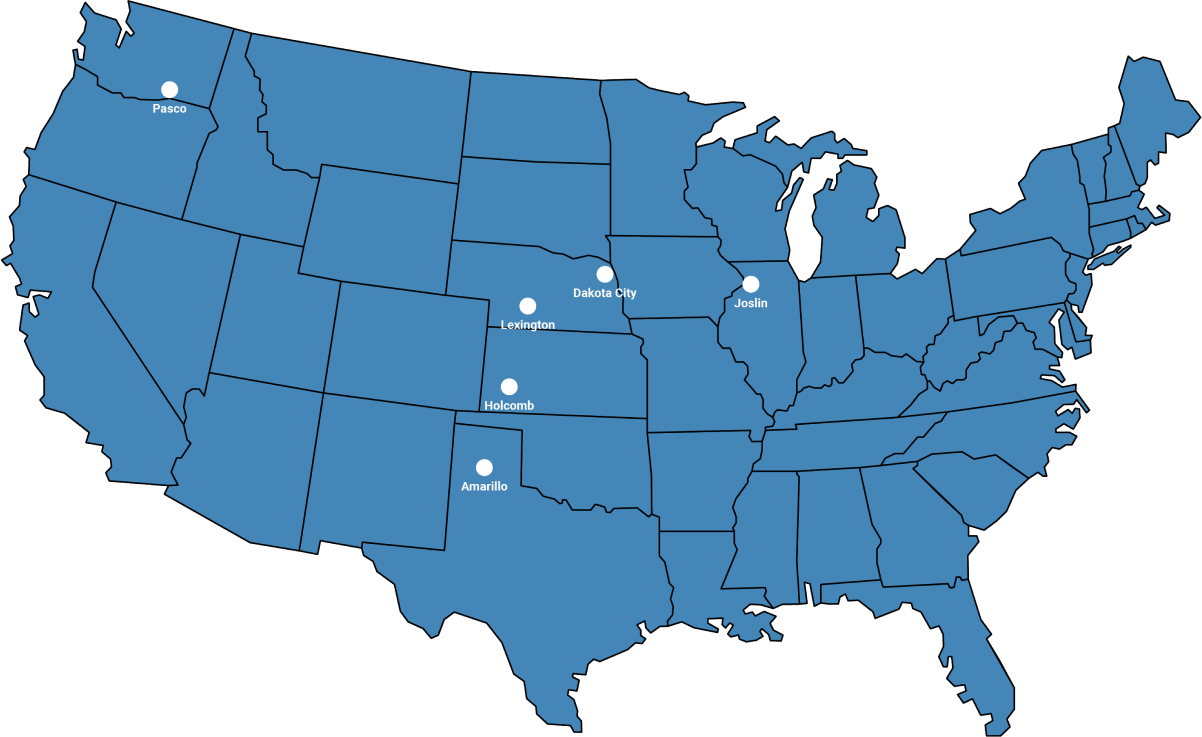
“The customer saw immediate gains in production throughput, with more meat being produced in less time.”
Looking Ahead
This partnership has demonstrated the power of innovation in solving real-world challenges in food production. The success of the BORR system not only resolved our customer’s immediate concerns regarding safety and efficiency but also paved the way for future collaboration between the two companies.
We continue to explore opportunities to integrate more automation and innovative technology into future production processes. As the food production industry evolves, Rome’s BORR system is a prime example of how forward-thinking solutions can drive both productivity and safety improvements.
Conclusion
Rome Grinding Solutions’ Bolt-on Retaining Ring (BORR) system has proven to be a game-changer. By addressing the dual challenges of production inefficiencies and worker safety, Rome helped increase production throughput while ensuring a safer environment for workers.
As food production companies continue to scale their operations, innovations like the BORR system will be key to maintaining competitive advantage, enhancing workplace safety, and optimizing production processes across all facilities.
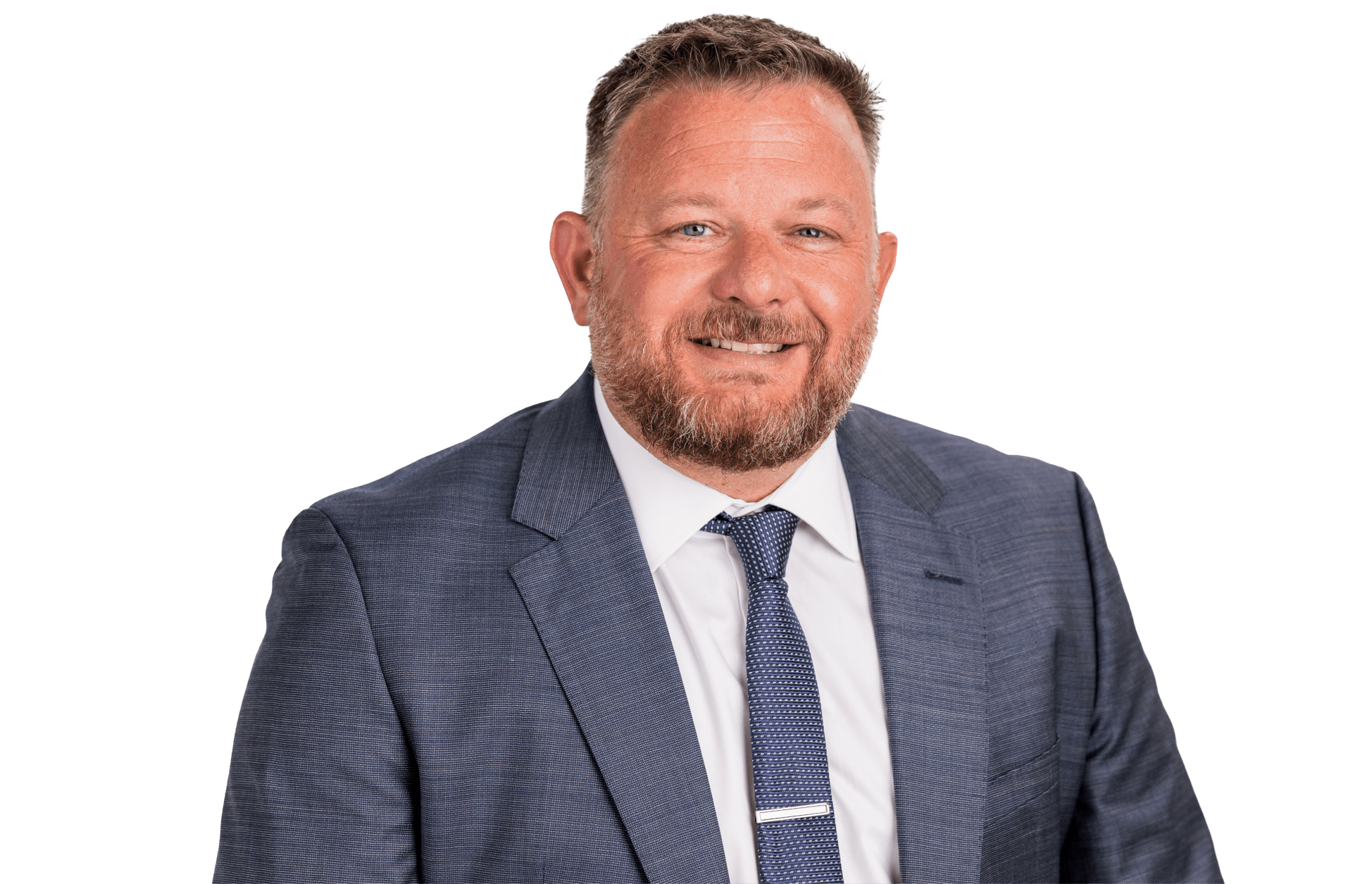
Connect With a Rome Expert
1427 Western Avenue
Sheldon, IA 51201
PO Box 186
800-443-0557