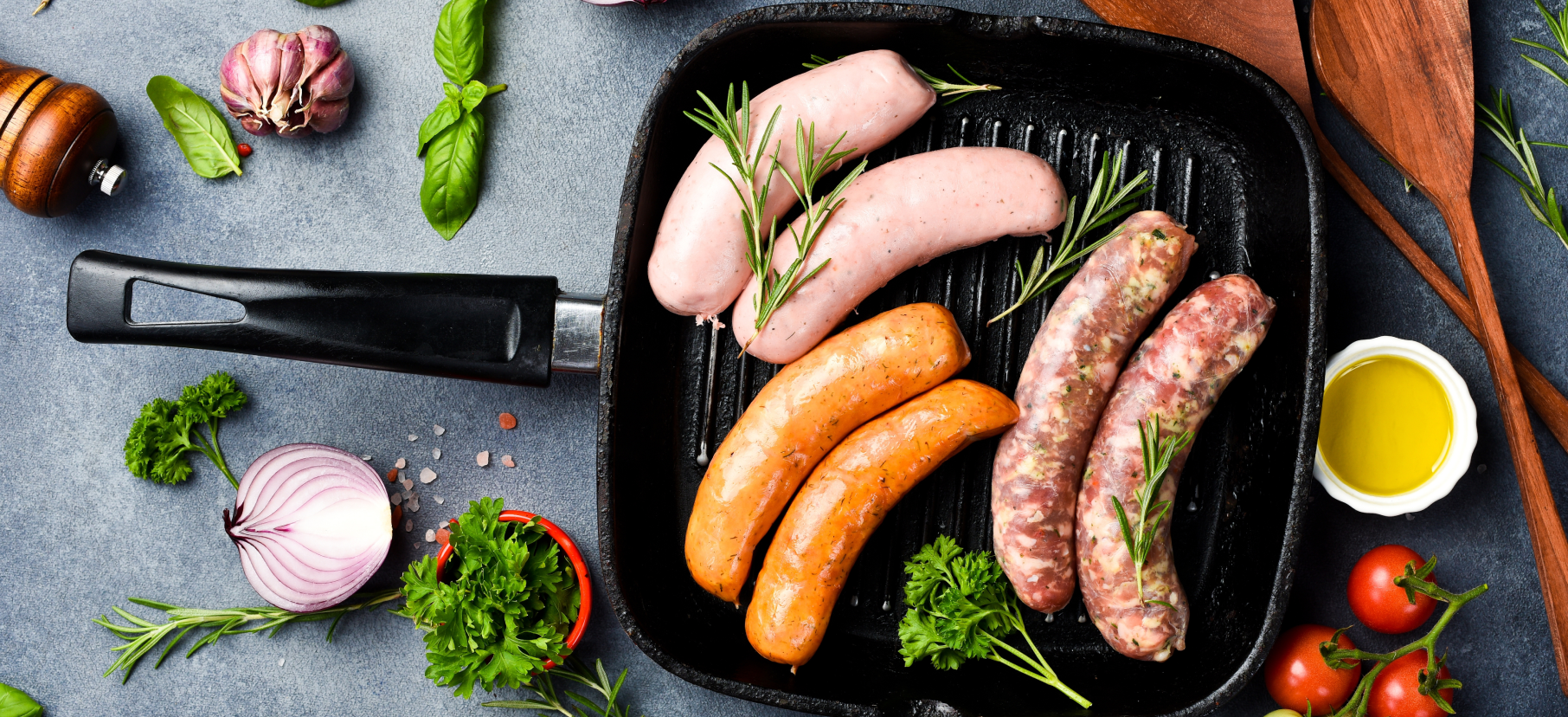
INTRODUCTION
A family-owned business based in New Jersey has been crafting high-quality artisan sausages for decades. Known for its commitment to tradition and quality, this Rome Grinding Solutions customer supplies products to retailers and restaurants across the U.S. They pride themselves on using time-honored methods to create sausages that families love.
THE Challenge: Maximizing Efficiency in a Tight Space
In 2023, the customer faced a unique operational challenge. Their facility required a new, high-capacity grinder to meet increased production demands, but space was at a premium. The designated area for the new grinder measured only four feet wide by twelve feet long, with a ten-foot ceiling height further constrained by a hoist system for bucket loading.
Initially, the customer considered a side-mount grinder, but it quickly became clear that this solution wouldn’t fit within the limited width of their processing area. The team needed a custom solution that could work within their constraints while maintaining their high standards for product quality and safety.
“By reducing the standard leg length of the Brutus 8 Grinder by three inches, Rome ensured that the grinder fit comfortably under the hoist system while maintaining optimal performance.”
The Solution: A Custom Grinder Designed for Precision and Fit
Rome Grinding Solutions stepped in to provide the perfect answer to these space and production needs. After initial consultations and a site visit to measure the facility, Rome’s team worked closely with the customer to design a custom version of the Brutus 8 Grinder with several key modifications, including shortened leg length, a custom hopper extension and belt guard as well as removable safety bars.
By reducing the standard leg length of the Brutus 8 Grinder by three inches, Rome ensured that the grinder fit comfortably under the hoist system while maintaining optimal performance. A tailored hopper extension was created to accommodate the bucket hoist system, allowing seamless loading without compromising safety. Rome also designed a custom belt guard to ensure the equipment remained within the confined space while adhering to strict safety standards. To meet the customer’s hygiene requirements and facilitate cleaning, Rome engineered removable safety bars inside the hopper. Unlike traditional welded safety bars, these could be easily taken out for maintenance, ensuring that the grinder remained sanitary and easy to clean.
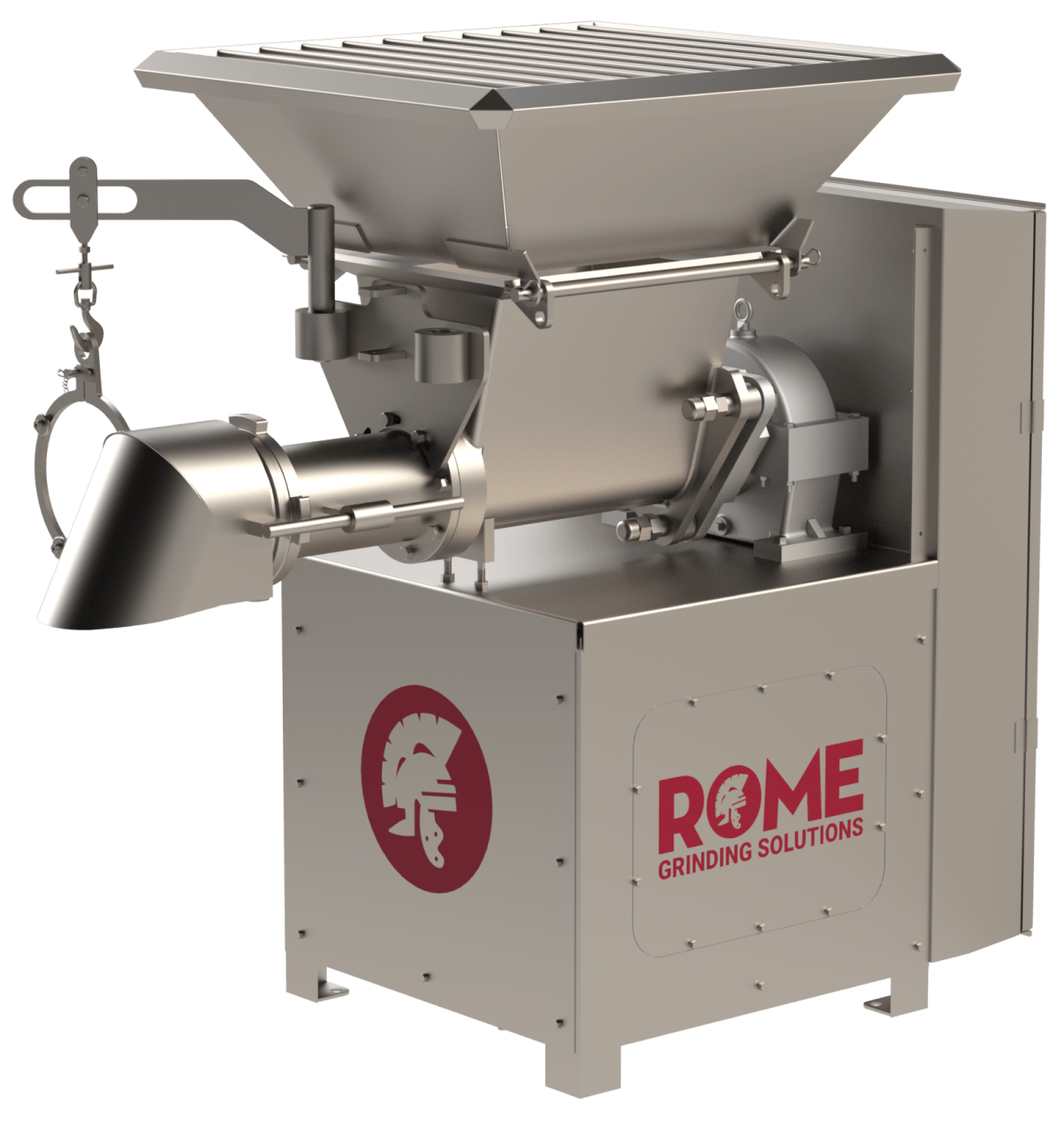
Implementation and Results
The finalized grinder was delivered in June 2024, with installation and startup following in July 2024. After some minor facility adjustments, the grinder was fully operational and immediately began to make an impact.
The custom grinder provided the capacity needed to meet growing demand, without sacrificing product quality. The custom design fits perfectly within the limited space, improving the efficiency of their production process. The integrated safety shield, custom belt guard, and removable safety bars ensured that the grinder met the company’s rigorous safety and sanitation standards.
Rome Grinding Solutions continues to provide support to this customer with routine visits to ensure the grinder operates at peak performance. These visits also include operator training to maximize the equipment’s efficiency and longevity.
The customer has expressed its satisfaction with the custom grinder solution, noting its superior performance and how it seamlessly fits into their production environment. The grinder’s durability and ease of maintenance have allowed them to maintain their commitment to quality while scaling up operations.
Conclusion
This project highlights Rome Grinding Solutions’ ability to tailor equipment to meet unique customer needs. By working closely together, Rome not only delivered a custom grinder that fit the physical constraints of their facility but also upheld the high product quality the customer is known for.
Looking for a custom solution to meet your food processing challenges? Contact Rome Grinding Solutions today to learn how we can help you optimize your operations.
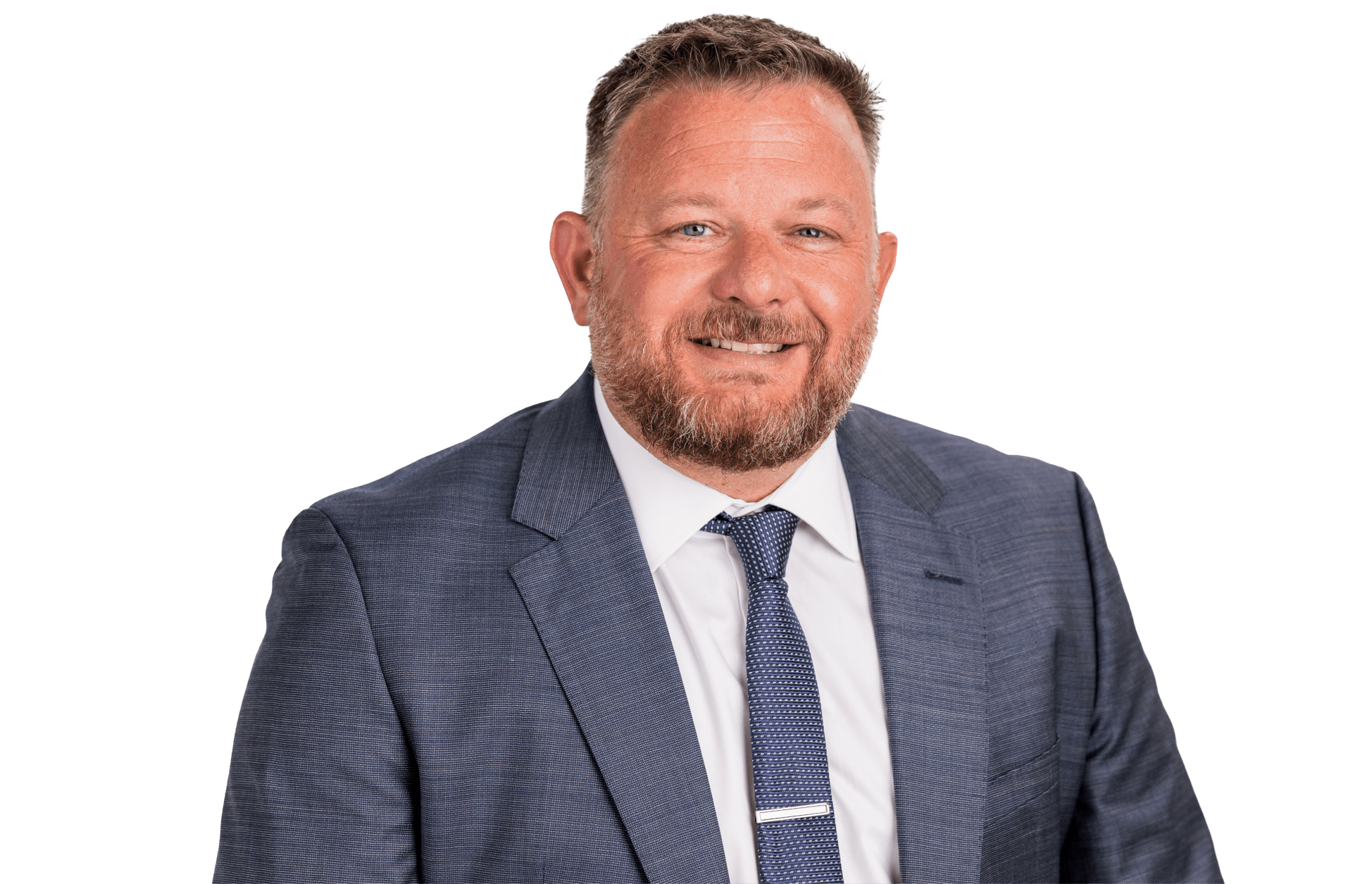
Connect With a Rome Expert
1427 Western Avenue
Sheldon, IA 51201
PO Box 186
800-443-0557